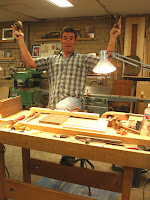
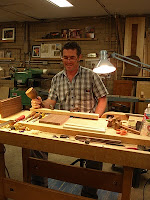
So I'm maybe three quarters into this piece, it's time to reflect. I will be at the Tucson art fair December 10-12 and will take this piece with me. I've had some people tell me to consider making smaller, knick knack things to sell, money is tight, people want cheaper stuff. Where does that leave craftsmanship? Will our economy squash things that are made well? Can consumers shift the idea of bargain versus investment? Will longer lasting, better made objects survive the consumer washout? I have customers who have owned a piece of mine for ten years and they understand that the piece just gets better with age, the patina wood develops takes time, the strength of the joints is evident in its durable stance. The design is a friendly reminder every day of the good decisions the woodworker made and the reasons we are drawn to the design, we are finally ready to have something made that we can be proud to own.This is an investment not only for our own living room today, but in an American way of life, craftsmanship is part of our history, part of why we are proud, and part of what we will be proud to pass on to our kids, not only the fabulous piece itself but the decision to purchase it and be part of the revolution.